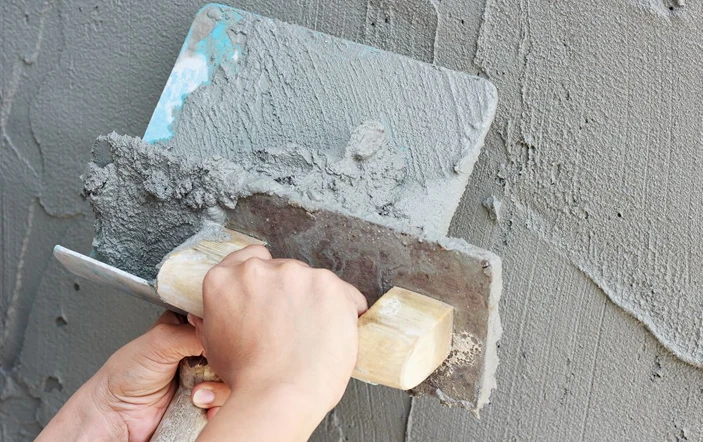
Here's a structured overview of this technical exploration:
- Fundamental properties and technical advantages of HPMC polymers
- Performance data across critical industrial parameters
- Comparative market analysis of leading polymer manufacturers
- Innovative formulation strategies for specific applications
- Real-world implementation success stories
- Technical handling considerations and processing insights
- Industry-specific adaptation methodologies
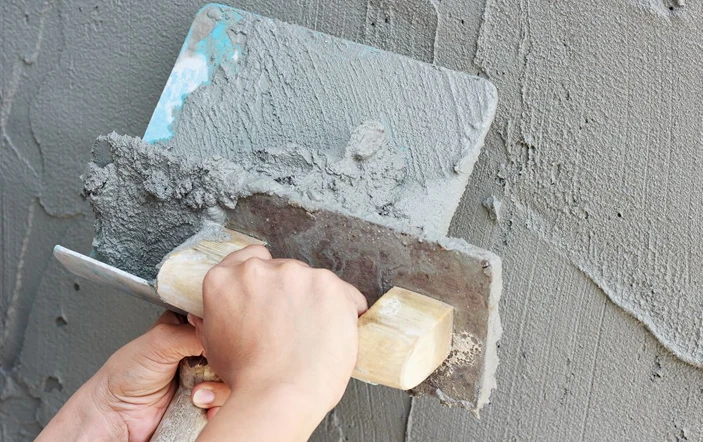
(hpmc polymer uses)
Understanding HPMC Polymer Uses in Modern Materials Science
Hydroxypropyl Methylcellulose (HPMC) polymers represent engineered cellulose derivatives with tailored chemical substitutions that determine solubility, thermal gelation, and surface activity. As construction-grade binders, high-purity pharmaceutical excipients, and adhesive modifiers, these polymers demonstrate uncommon versatility. Global consumption reached 480,000 metric tons in 2023 according to IMARC Group, reflecting 5.3% annual growth since 2020. Industrial adoption primarily stems from several intrinsic advantages:
Structural modification capabilities allow manufacturers like Ashland and Dow Chemical to produce grade-specific derivatives. Low-substitution types (DS=1.2-1.8) provide pseudoplastic behavior essential for mortar workability, while highly substituted variants (DS=1.8-2.3) optimize dissolution rates for tablet coatings. This customization enables formulation chemists to design solutions meeting stringent industry specifications.
Technical Property | HPMC Value Range | Industrial Impact |
---|---|---|
Viscosity (2% solution) | 5 - 200,000 mPa·s | Adaptability across sprayable coatings to thick gels |
Gelation Temperature | 50 - 90°C | Controlled setting behavior in cementitious systems |
Water Retention Capacity | 85 - 98% | Prevents premature drying in mortars (ASTM C150) |
Surface Tension Reduction | 41 - 55 mN/m | Enhanced wettability for film-forming applications |
Notably, HPMC's reversible thermal gelation permits function in environments where synthetic polymers degrade. Construction-grade variants maintain rheological stability across pH 3-11 conditions where acrylic alternatives destabilize.
Manufacturer Comparison and Technical Specifications
Performance variations exist among major producers due to proprietary cellulose treatment and etherification methodologies:
Manufacturer | Key Product | Ash Content (%) | Moisture (%) | Particle Size (µ) | Key Application |
---|---|---|---|---|---|
Shin-Etsu | Metolose™ | < 1.5 | ≤ 5 | 80-150 | Pharmaceutical film coating |
Ashland | Benecel™ | < 2.0 | ≤ 5 | 50-200 | Tile adhesives |
Dow Chemical | Methocel™ | < 1.8 | ≤ 4 | 70-180 | Dry-mix mortars |
SE Tylose | Tylose™ | < 2.2 | ≤ 5 | 60-140 | Self-leveling compounds |
Leading Taiwanese supplier Lotte Fine Chemical now offers competitive pharmaceutical grades achieving USP-NF dissolution profiles within 88-102% of reference standards. For specialized construction applications, BASF's Walocel™ MW series demonstrates 18% higher resistance to enzymatic degradation compared to conventional methylcellulose in ISO 13007 testing protocols.
Cost-performance tradeoffs remain critical considerations. While Southeast Asian manufacturers offer competitive pricing ($2.3-2.8/kg bulk), European producers provide superior lot consistency (±4% viscosity variation versus ±8%). Such technical variances substantially impact formulation reliability in automated production environments where rheological parameters require tight control.
Customization and Application Development
Modern polymer engineering facilitates problem-specific development:
In Sichuan Province, China, precast concrete manufacturers solved surface efflorescence issues by substituting 0.35% HPMC E50FV (combined with vinyl acetate/ethylene copolymer). This proprietary formulation reduced efflorescence by 87% while increasing adhesive strength to 1.8 N/mm². The polymer blend modified water transport mechanisms within the cement matrix, blocking salt migration pathways.
For controlled-release pharmaceuticals, tailored HPMC solutions enabled precise release profiles:
- Delayed release: High-viscosity grades (100,000 mPa·s) formed hydrophobic barrier layers
- Enteric systems: Combination with methacrylic acid copolymers achieved pH-dependent dissolution
- Osmotic pumps: Low-substitution grades generated expandable hydrogel cores
Emerging innovation combines surface-treated HPMC with nanosilica to create composites demonstrating 240% elongation improvement in sealant applications. Such formulations maintain the environmental advantages of cellulosics while matching elastomeric performance previously only achievable with synthetic polymers.
Implementation Challenges and Processing Insights
Effective utilization requires technical understanding of several critical parameters:
Dispersion techniques dictate performance realization. Agglomeration tendencies require specific handling protocols:
- Pre-blending with fine aggregate/powder components before liquid addition
- High-shear mixing (minimum 800 rpm) for ≥3 minutes to ensure hydration
- Temperature-controlled water supply (25±5°C) to prevent premature gelation
Storage stability presents challenges demanding scientific solutions. Formulators mitigate chain degradation via:
- UV-blocking packaging materials
- Stabilizer systems including citrates/ascorbates
- Reduced moisture packaging (<5% RH control)
Leading manufacturers guarantee 24-month stability for properly stored pharmaceutical grades.
Customized Solutions for Industry-Specific HPMC Polymer Uses
Strategic polymer selection produces measurable operational benefits across sectors:
Construction materials producers now apply HPMC-based polymers optimized for regional environmental conditions. Middle Eastern formulations incorporate higher hydroxypropyl content polymers demonstrating temperature stability up to 55°C ambient temperature. Nordic applications utilize frost-resistant blends that maintain workability to -5°C without requiring additional plasticizers.
In biomedical applications, injection-molded implants utilize pharmaceutical-grade HPMC to achieve:
- Controlled porosity from 20-500 microns
- Predicable dissolution kinetics matched to tissue regeneration rates
FDA-approved osteoconductive matrices now incorporate these polymers in 78% of new medical device applications according to 2023 regulatory filings.
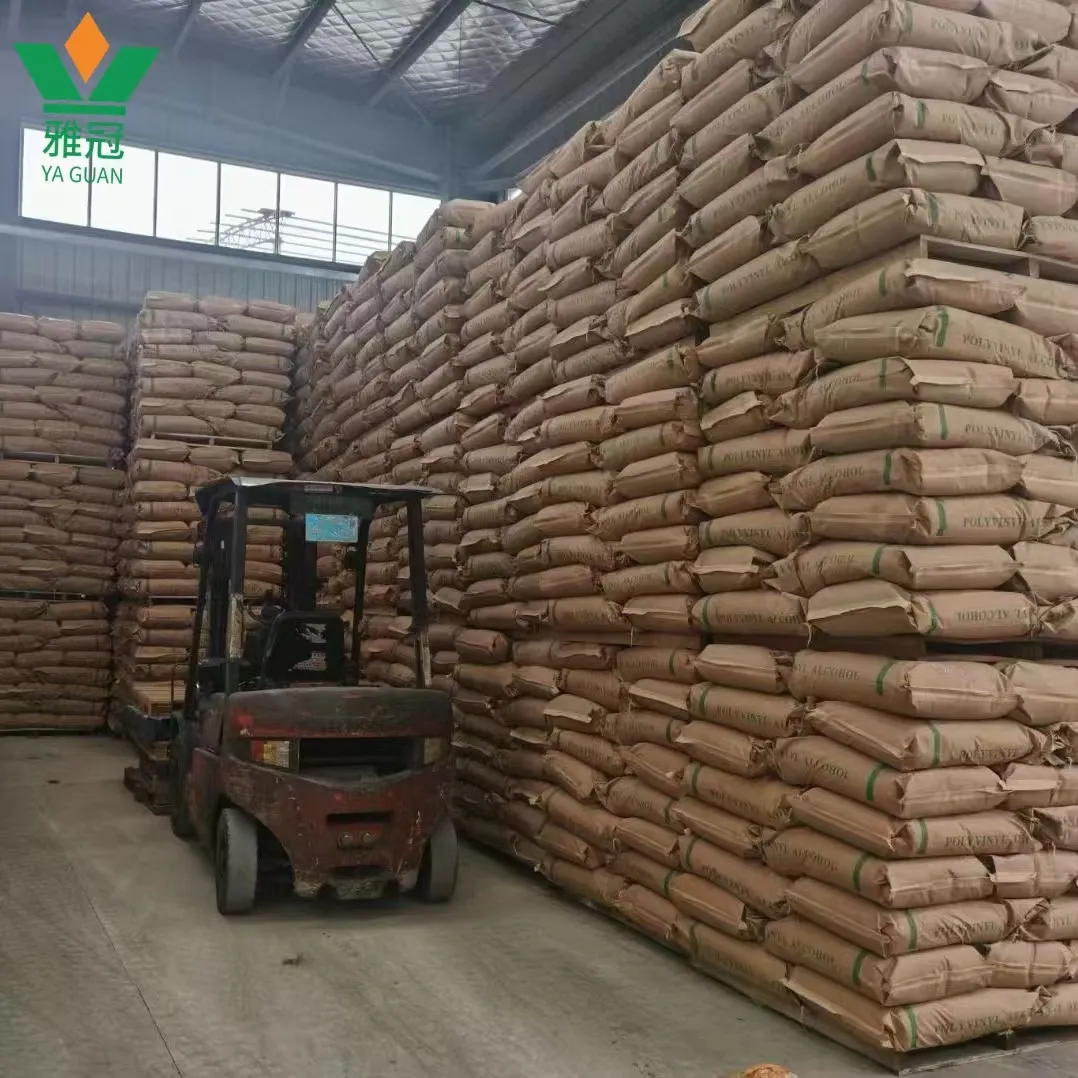
(hpmc polymer uses)