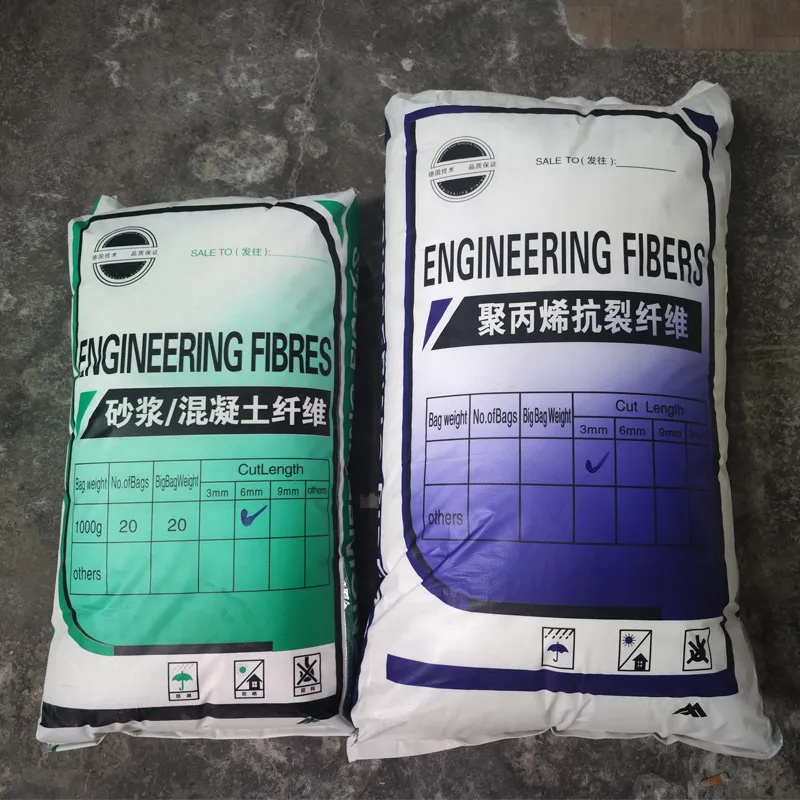
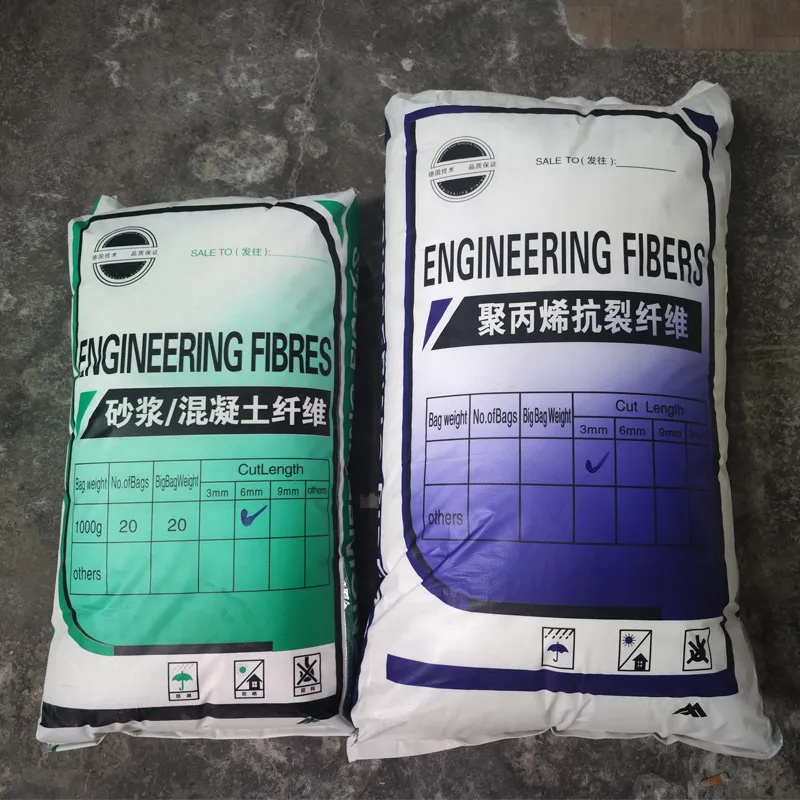
Polypropylene Fiber (PP Fiber) stands at the forefront of modern reinforcement technology, influencing infrastructure, composite materials, and high-performance manufacturing. With evolving industry demand for durability, corrosion resistance, and eco-efficiency, Polypropylene Fiber is a strategic material across petrochemical, metallurgy, civil engineering, water treatment, transportation, and construction industries.
- ISO/TC 61 & ASTM C 1116/C1116M guidelines endorsed
- Leading R&D spanning over 15 years experience
- Compliant with RoHS, ANSI, and EN 14889-2:2006 standards
1. Industry Trends: The Rise & Evolution of Polypropylene Fiber
- Key Drivers: Growing infrastructure investments, sustainability mandates, and the surge for advanced composites.
- Sector Adoption: Construction (47%), industrial filtration (18%), automotive (16%), medical textiles & hygiene (9%), packaging (6%), others (4%).
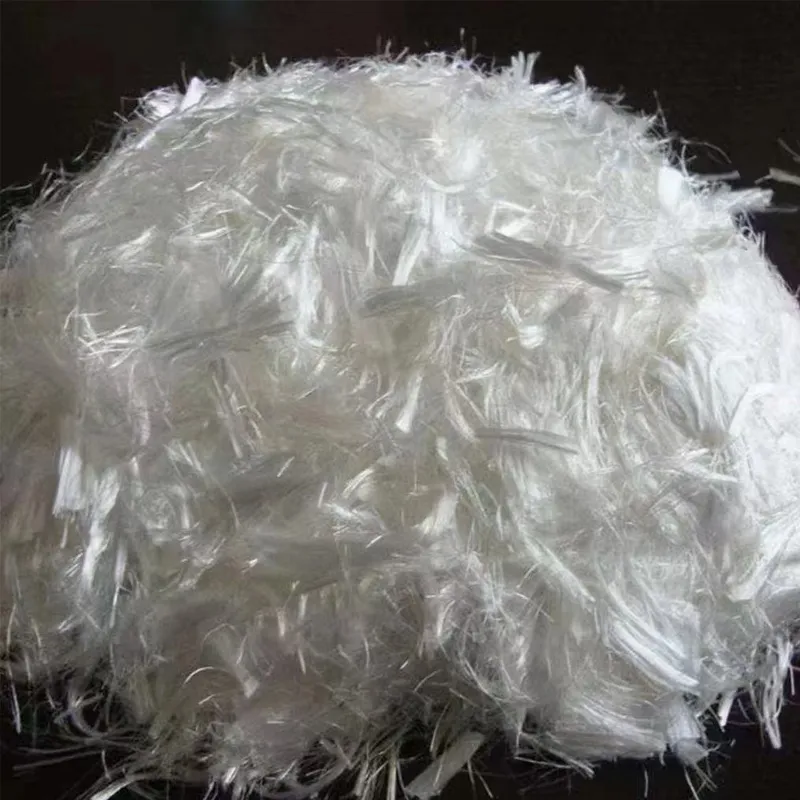
2. Manufacturing Process: Polypropylene Fiber Production Explained
2.1 Technical Process Flowchart
- Resin Selection: Polypropylene homopolymers or copolymers with melt flow index 2-5 g/10min
- Melting Temperature: 165°C - 170°C, ensuring isotacticity for maximum crystallinity
- Spinning: Controlled die-head and quenching conditions achieve monofilament or fibrillated structures
- Cutting & Finishing: Precision length (3mm-54mm), denier (1.5d-7d), & optional surface coating
- Testing: In-house labs conforming to ISO 2062, ASTM D2256, EN 14889-2
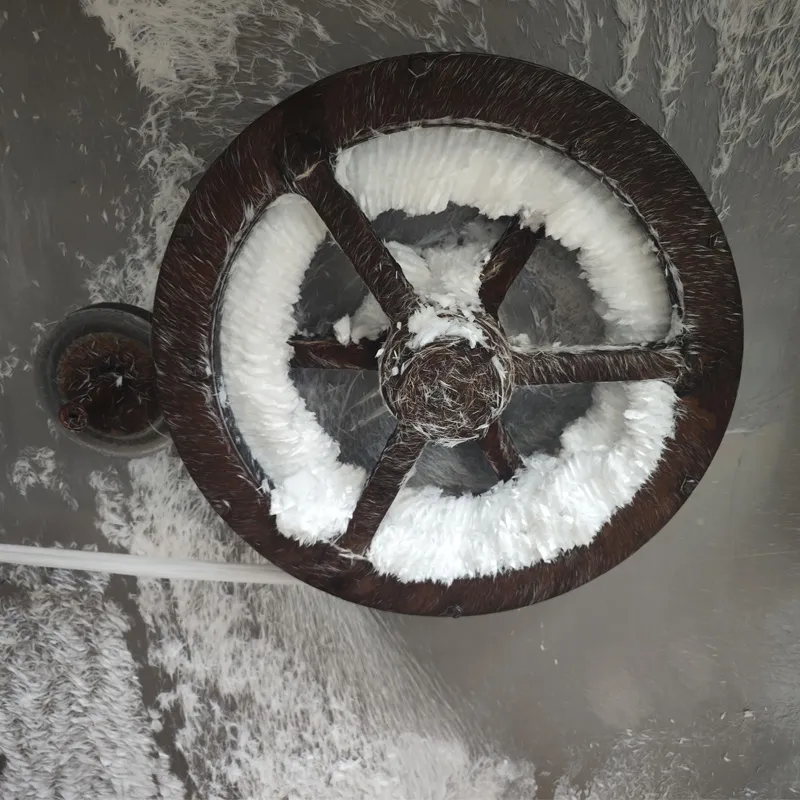
3. Technical Parameters & Product Specification Table
Parameter | Value | Standard/Note |
---|---|---|
Material | Virgin Polypropylene (PP), Isotactic content > 95% | ISO 1873-1:2022 |
Denier/Line Density | 1.5 – 7.0 dtex | DIN EN ISO 2060 |
Cut Length | 6mm, 12mm, 19mm, 54mm | Customizable |
Tensile Strength | ≥ 450 MPa | ISO 2062 |
Elongation at Break | 15–25% | ISO 2062 |
Modulus of Elasticity | > 4,500 MPa | ASTM D638 |
Density | 0.91 - 0.93 g/cm³ | ASTM D792 |
Melting Point | 165-170°C | ISO 11357-3 |
Chemical Resistance | Excellent (acids, alkalis, salts), non-corrosive | LAB Tested |
Durability | 30+ years (in concrete, bitumen, geo-composites) | Field Data |
3.1 Polypropylene Fiber vs. Other Synthetic Fibers: Product Comparison Table
Fiber Type | Density (g/cm³) | Tensile Strength (MPa) | Chemical Resistance | Melting Point (°C) | Durability | Cost Index |
---|---|---|---|---|---|---|
Polypropylene Fiber | 0.91 | 450-600 | Excellent | 165-170 | 30+ yrs | 1 |
Nylon Fiber | 1.14 | 650-850 | Good | 220-260 | 20+ yrs | 1.75 |
Polyester Fiber | 1.38 | 500-900 | Moderate | 250-260 | 20-25 yrs | 1.3 |
Glass Fiber | 2.55 | 1500-2000 | Poor (alkali) | 850 | 20+ yrs | 2.5 |
Steel Fiber | 7.85 | 1100-2850 | Corrosive | 1450 | 15+ yrs | 3.1 |
4. Visual Data Analysis: Trend Charts & KPI Visualization
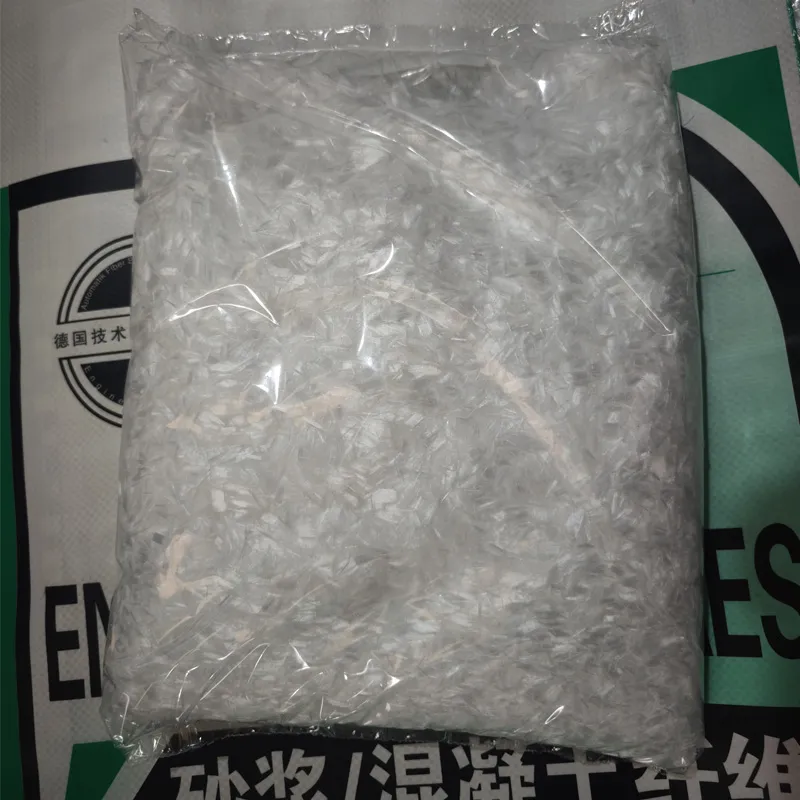
5. Key Advantages of Polypropylene Fiber
- Ultra-high chemical resistance: Unaffected by chlorides, sulfates, acids, alkalis. No corrosion, rust, or rotting risk.
- Lightweight: Lower density (0.91g/cm³) leads to economy in mixing and transport.
- Non-magnetic & Inert: No effect on electrical fields, no alkali-aggregate reactions in concretes.
- Thermal Stability: Serviceable up to 110°C short-term, melting point around 165-170°C; resists shrinkage cracking in composites.
- Long Service Life: Field data supports 30–50 years stability in concrete, bitumen binders, and geotechnical layers.
- Ease of Dispersion: Available in monofilament, fibrillated mesh, staple cut – rapidly homogenizes in all matrixes.
- Cost-effective: Superior performance-to-cost for reinforcement compared to steel or nylon alternatives.
- Eco-certified: Meets RoHS and SVHC requirements (independent SGS test reports available).
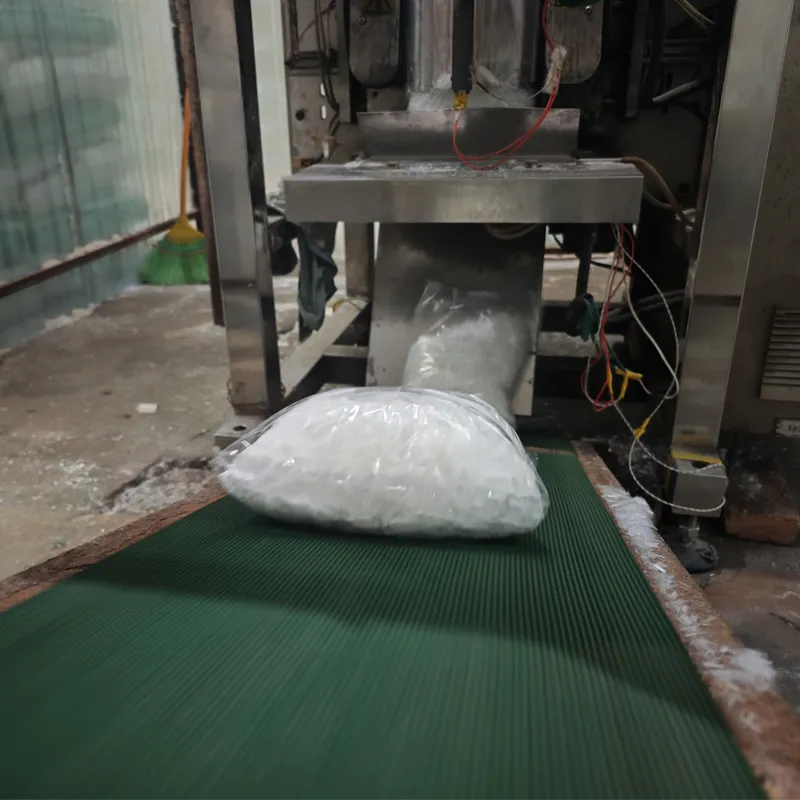
6. Major Suppliers & Brand Comparative Review
- Yaguan (Polypropylene Fiber): ISO 9001 certified, >15 years export experience. Custom cut. Durability-focused. Quick delivery.
- Sika AG (SikaFiber®): Top EU demand, main focus on concrete reinforcement, fully EN 14889-2 compliant.
- BASF (MasterFiber): Premier quality. Dense R&D. In-depth technical support for large-scale civil projects.
- Owens Corning: Diverse synthetic range. US/Canada centric. Focused on geo-compositions.
- UltraFiber: Custom color/cut, primarily for thin section concrete.
- Others (Quanzhou, Fosroc, Propex): Varied ISO/ANSI/EN certifications; broad region OEMs for competitive pricing.
Supplier/Brand | Region | ISO Cert. | Customizable Spec. | Main Application | Support & Price |
---|---|---|---|---|---|
Yaguan | Asia, Europe, Americas | ISO 9001, EN 14889 | Yes (cut/denier/surface) | Construction, filtration, composites | 5★ | Competitive |
SikaFiber® | Europe, APAC, US | ISO 14001 | Moderate | Concrete | 4★ | High |
MasterFiber® | EU, US | ISO/EN/ASTM | Limited | Concrete/repair | 4.5★ | Premium |
UltraFiber | US, LATAM | ISO 9001 | Excellent | Thin slabs, overlays | 4.3★ | Medium |
7. Customization & Turnkey Support Solutions
- Custom length & denier: 3mm–54mm, 1.0–8.0 dtex options for batch orders (MOQ: 100kg/project spec sheet required).
- Tailored surface treatments: Hydrophilic, anti-static, flame retardant per client matrix compatibility.
- Color-matching: Natural white, UV-resistant black, or customer-specified shades.
- Private labeling/OEM: Available for industrial distributors and branded construction material providers.
- Technical on-site support: Mix design, installation training, and post-application evaluation (certified consultants).
Warranty: 24-month product performance guarantee (no fiber deterioration in standard construction environments).
8. Application Scenarios & Case Studies: Polypropylene Fiber in Action
8.1 Concrete Reinforcement & Anti-Cracking
Deploying Polypropylene Fiber in concretes enables a reduction of plastic shrinkage cracks by over 60%. A 2022 project in Singapore's MRT tunnel lining used 0.7% Polypropylene Fiber dosage, resulting in:
- Increased flexural strength (from 5.5 MPa to 8.9 MPa)
- No fiber balling, rapid mix dispersion
- Excellent post-cracking ductility even after 5-year service (field cores tested)
8.2 Geotextiles & Waterproofing Membranes
China's South-to-North Water Diversion, e.g., utilizes high-tenacity Polypropylene Fiber for geotube reinforcement, extending service life under aggressive chemical environments.
8.3 Asphalt & Bitumen Modification
Polypropylene Fiber addition in road asphalts increases rutting resistance by 35%, boosts elasticity modulus, and significantly enhances lifespan against freeze-thaw cycles.
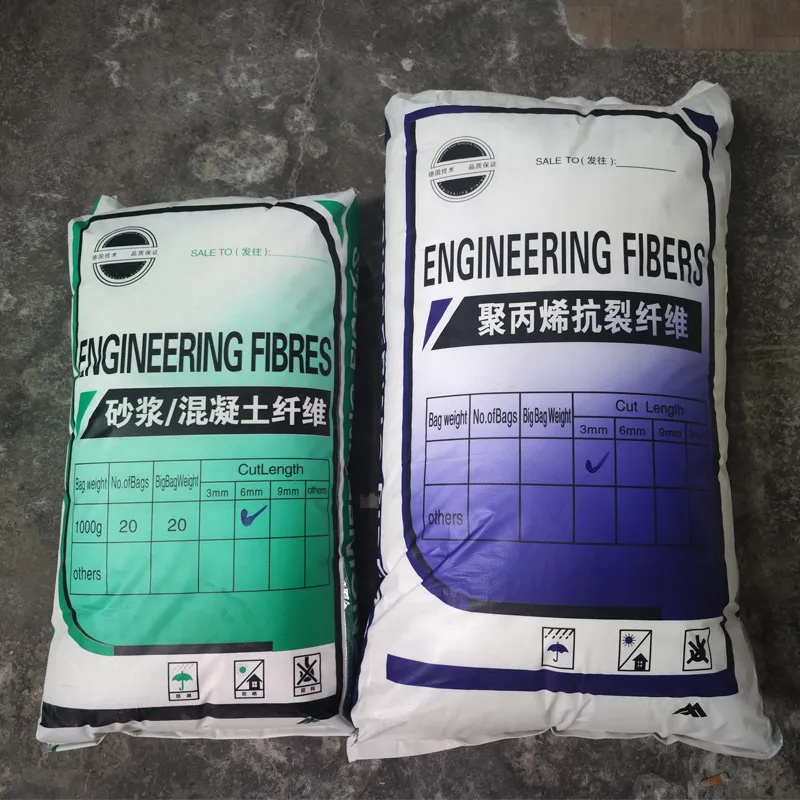
8.4 Client Feedback & Partner Cases
Client 2, Indian Waterworks: “The PP fiber layer in geomembrane dams remained intact after five monsoons, outperforming older polyester meshes.”
Client 3, Asphalt Engineering (Vietnam): “Road rutting reduced by 30%, visible after just two years. No fiber exposure, zero surface peeling.”
Partner Firms: Arab Contractors (Egypt), Gammon (Singapore), Cemex (global), VINCI (EU).
9. FAQs & Expert Answers: Polypropylene Fiber Terminology
- Q1. What is the material base of Polypropylene Fiber?
- Polypropylene Fiber is produced from isotactic polypropylene pellets, which grant it exceptional chemical resistance and mechanical stability for construction and industrial applications.
- Q2. What are common fiber forms and specifications?
- Available as monofilament (1.5–5 dtex), fibrillated mesh, or staple (cut: 3–54mm); denier, cut length, and type can all be customized for matrix compatibility.
- Q3. Which standards must Polypropylene Fiber meet?
- Industry standards such as ISO 2062, EN 14889-2:2006, ASTM C1116 apply to tensile strength, performance in concrete, and durability under extended service.
- Q4. Is Polypropylene Fiber environmentally friendly?
- Yes. It is non-leaching, non-toxic, and recyclable. It’s compliant with RoHS and REACH (SVHC) requirements.
- Q5. How is Polypropylene Fiber installed in concrete?
- Fibers disperse rapidly with standard mixing—no special equipment needed. Dosage: 0.7–1.5kg/m³ typical for concrete, depending on crack control/impact needs.
- Q6. Can Polypropylene Fiber be used in potable water or food-contact scenarios?
- Yes, food-grade and potable-water applications use fibers manufactured to FDA and EU 10/2011 guidelines – ask for relevant test reports.
- Q7. What is the typical delivery, warranty, and support for bulk orders?
- Standard delivery is 7–10 days for catalogue items, 12–18 days for custom specs. Warrantee of 24+ months. Technical and after-sales support by certified specialists.
10. Conclusion & Industry Perspectives
Polypropylene Fiber has fundamentally transformed reinforced materials engineering thanks to its eco-credentials, cost-performance, and multi-sector adaptability. Ongoing research—see ScienceDirect or the

Pervious