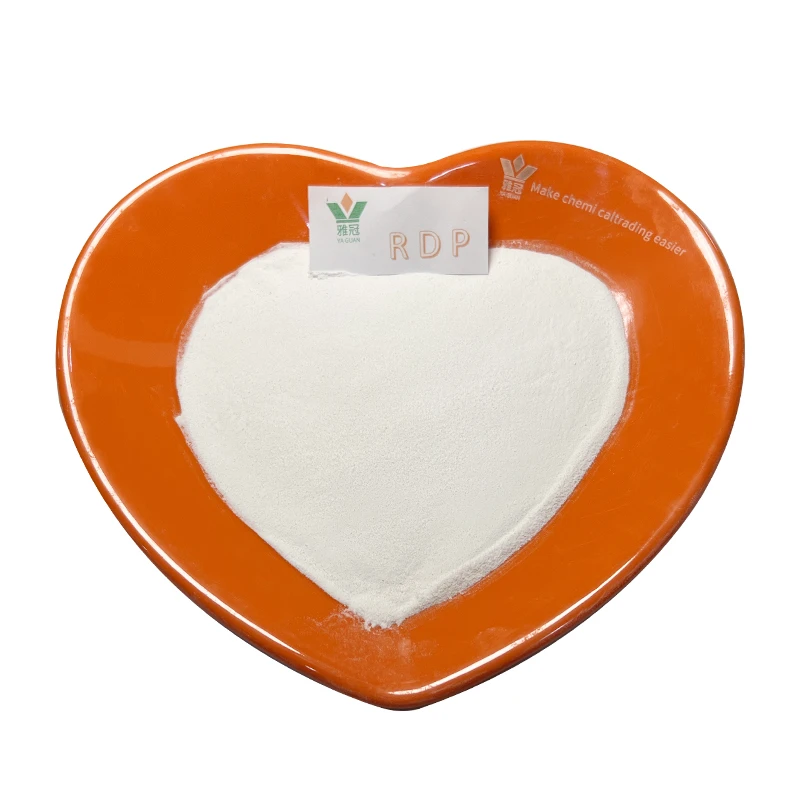
- Introduction and Importance of Polycarboxylic Acid Superplasticizer in Modern Construction
- Technical Superiority and Mechanism of Polycarboxylic Ether Polymer
- Role of Calcium Formate Derived from Formic Acid in Enhancing Performance
- Market Data and Industry Demand Analysis
- Comparative Analysis of Leading Manufacturers
- Customized Polycarboxylic Acid Superplasticizer Formulation Solutions
- Case Studies and Future Outlook for Polycarboxylic Acid Superplasticizer Technologies
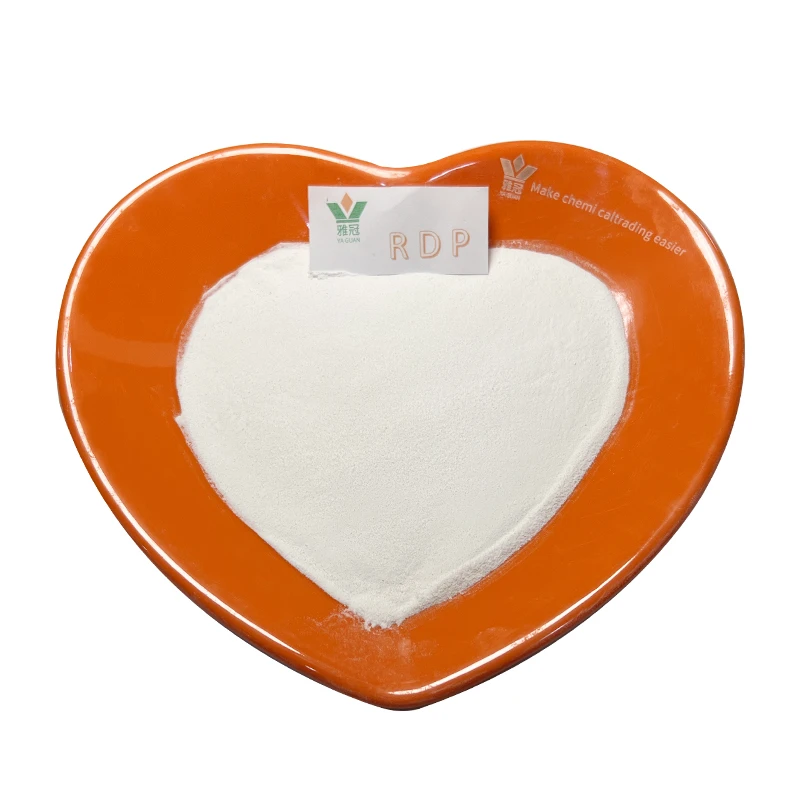
(polycarboxylic acid superplasticizer)
Introduction: The Impact of Polycarboxylic Acid Superplasticizer on Concrete Technology
Polycarboxylic acid superplasticizer is redefining concrete admixture technology. Engineered to considerably improve concrete’s workability and strength while reducing its water content, this advanced superplasticizer enables the construction industry to meet demanding architectural and sustainability standards. Over the past decade, the market for high-performance concrete admixtures has grown at an annual rate exceeding 8%, motivated by increased urban development and stricter building codes. Recent research highlights that incorporating polycarboxylic acid superplasticizer
can reduce water demand by up to 30% without compromising mechanical integrity. Such improvements have significant implications—not only for engineers aiming for more robust structures but also for stakeholders committed to sustainable development practices.
Technical Superiority of Polycarboxylic Ether Polymer in Concrete Applications
At the heart of polycarboxylic acid superplasticizer’s remarkable performance lies its polycarboxylic ether polymer backbone. Unlike traditional lignosulfonate or naphthalene-based reducers, the polycarboxylic ether polymer’s comb-like molecular structure provides highly effective dispersion of cement particles. This attribute drastically enhances particle separation, decreases agglomeration, and produces a uniformly mixed, high-flowing concrete without segregation or bleeding. Furthermore, the molecular design allows for tailored side-chain lengths, rendering the product compatible with a wide range of cement types and mineral admixtures. These polymers support concrete slump retention of over two hours—double the retention period achievable with older-generation superplasticizers. This technical advantage ensures greater on-site flexibility and reduces the risk of re-tempering or work delays.
Role of Calcium Formate from Formic Acid in Enhancing Concrete Performance
Integrating calcium formate derived from formic acid into concrete mixtures containing polycarboxylic acid superplasticizer introduces a strategic leverage point for performance tuning. Calcium formate acts as both an early strength enhancer and a set accelerator, countering the commonly observed extension of setting time associated with high-performance superplasticizers. When utilized synergistically, studies show a 15-25% increase in early compressive strength within 24 hours, facilitating faster demolding, accelerated project timelines, and improved cost efficiency. Moreover, calcium formate contributes to enhanced freeze-thaw durability and reduced porosity. Such dual-function admixture systems enable concrete producers to address project-specific needs more efficiently, providing enhanced value for infrastructure work in demanding climates.
Market Data and Demand Trends for Superplasticizer Admixtures
The global market for polycarboxylic acid superplasticizer is projected to reach USD 8.2 billion by 2027, driven by urbanization, infrastructure renewal, and the need for eco-friendly construction materials. Asia-Pacific accounts for over 45% of global consumption, led by China, India, and Southeast Asia. According to a 2023 market survey, "energy-efficient concrete formulations" is the top purchasing driver for over 60% of surveyed construction firms. Industry analysts attribute the widespread adoption to cost savings, improved durability, and compliance with LEED and other green building certifications. In addition, as regulations concerning concrete emissions and performance tighten globally, the industry’s shift toward next-generation admixtures such as polycarboxylic acid superplasticizer is expected to accelerate further.
Comparison of Leading Polycarboxylic Acid Superplasticizer Manufacturers
Selection of the right supplier is crucial for ensuring consistent performance, technical support, and innovation. The table below provides a comparative overview of four global manufacturers based on production capacity, product portfolio, R&D investment, and customer support.
Manufacturer | Annual Capacity (MT) | Product Variants | R&D Expense (% of Revenue) | Technical Support Quality |
---|---|---|---|---|
Company A | 120,000 | 14 | 6.8% | Excellent - 24/7 helpline, on-site assistance |
Company B | 80,000 | 9 | 4.9% | Good - Dedicated regional teams |
Company C | 135,000 | 17 | 7.2% | Excellent - Custom trials available |
Company D | 65,000 | 7 | 3.5% | Average - Web-based only |
The most advanced manufacturers focus on expanding product lines to include polycarboxylic acid superplasticizer formulations compatible with both high-performance and economic market requirements. Notably, higher investments in research and development directly correlate with more innovative, adaptable product offerings and better post-sale service.
Custom Formulation Solutions for Diverse Construction Needs
With construction projects becoming increasingly complex, a one-size-fits-all approach to admixtures is no longer viable. Leading suppliers of polycarboxylic acid superplasticizer offer bespoke formulation services tailored to the geographic, climatic, and technical context of each project. Customization parameters include setting time, slump retention, viscosity, chloride content, and compatibility with supplementary cementitious materials. By leveraging laboratory resources and field data, formulators can optimize admixture blends to solve challenges such as hot weather concrete placement, precast cycle acceleration, and marine structure longevity. Further, by adjusting the polycarboxylic ether polymer side chains or incorporating specialized additives like calcium formate, custom solutions can achieve performance targets in areas where off-the-shelf admixtures fall short. Case histories indicate up to a 20% improvement in compressive strength and a 25% reduction in permeability with tailored blends, compared to standard products.
Conclusion: Polycarboxylic Acid Superplasticizer in Future Modern Construction
Polycarboxylic acid superplasticizer stands at the forefront of concrete technology innovation. As the demand for sustainable, high-performance, and more resilient building solutions intensifies, its role will only become more central. Real-world implementation attests to its transformative impact: for example, the Xiamen International Conference Center utilized a customized superplasticizer-cement-calcium formate solution, resulting in a 22% increase in early-stage strength and remarkable long-term durability under marine conditions. Similarly, several major infrastructure projects reported faster project delivery and compliance with strict environmental regulations. Looking forward, advancements in polycarboxylic ether polymer chemistry, combined with precise admixture engineering, will further expand the boundaries of what modern concrete can achieve, supporting urbanization and infrastructure challenges worldwide with superior material science and tailored solutions.
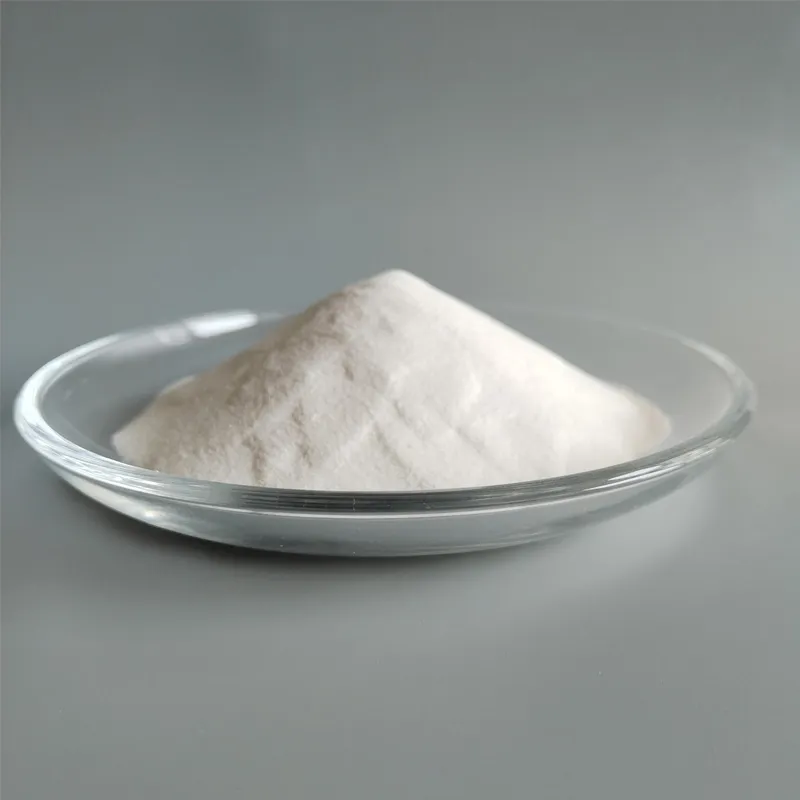
(polycarboxylic acid superplasticizer)
FAQS on polycarboxylic acid superplasticizer
Q: What is polycarboxylic acid superplasticizer?
A: Polycarboxylic acid superplasticizer is a high-performance water-reducing agent widely used in concrete production. It helps improve workability and strength by dispersing cement particles. This results in reduced water demand and better concrete quality.
Q: How is calcium formate produced from formic acid?
A: Calcium formate is produced by reacting formic acid with calcium carbonate or calcium hydroxide. This reaction yields calcium formate and water. Calcium formate is commonly used as an accelerator in construction materials.
Q: What are polycarboxylic ether polymers used for?
A: Polycarboxylic ether polymers are primarily used as base materials for polycarboxylic acid superplasticizers. They provide excellent dispersing ability in cement mixtures. Their use enhances concrete fluidity and strength.
Q: Why use polycarboxylic acid superplasticizer in concrete?
A: Using polycarboxylic acid superplasticizer significantly improves concrete workability and strength. It allows for lower water-cement ratios, leading to durable concrete. It also reduces energy consumption during mixing.
Q: What is the difference between polycarboxylic acid superplasticizer and traditional superplasticizers?
A: Polycarboxylic acid superplasticizers offer better water reduction and consistency than traditional types like naphthalene or melamine-based superplasticizers. They provide longer slump retention and lower dosage requirements. This makes them ideal for modern concrete applications.