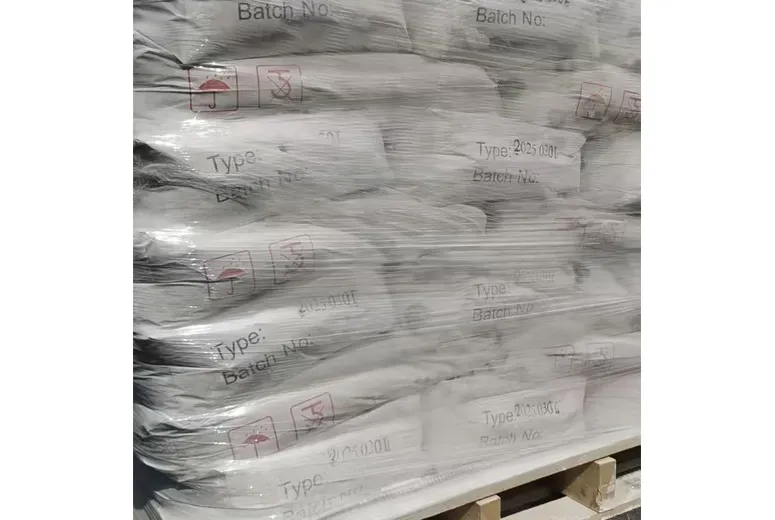
- Introduction to PVA for Painting: Definition and Importance
- Technical Advantages of PVA in Paint Applications
- Comparative Analysis: PVA vs. Other Primers for Walls and Concrete
- Manufacturers and Product Quality Comparison
- Customized PVA Solutions for Painting Projects
- Real-World Application Cases Demonstrating Benefits
- Conclusion: Harnessing PVA for Painting for Superior Finishes
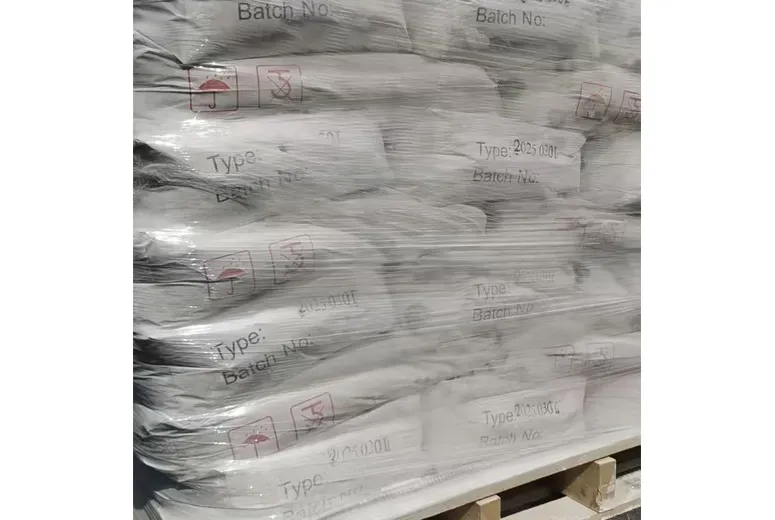
(pva for painting)
Introduction to PVA for Painting: The Foundation for Professional Results
In the realm of surface preparation, polyvinyl acetate (PVA) has cemented its role as a definitive enhancer for painting projects. PVA for painting serves as a bridging agent between substrates and topcoats, streamlining application and boosting adhesion for paints. This water-based synthetic polymer is renowned for its cost-effectiveness, low odor, and compatibility with a wide variety of surfaces. Contractors and DIY enthusiasts alike rely on PVA for priming plaster, drywall, masonry, and even bare concrete. Industry reports underscore its popularity, with more than 60% of professional painters specifying PVA as the primer of choice for internal wall and ceiling applications. Understanding the chemistry, application, and specific advantages of PVA-based primers is crucial for anyone seeking a durable, high-quality finish on walls or concrete surfaces.
Technical Advantages of Using PVA in Painting Applications
The use of PVA walls before painting provides numerous technological benefits that elevate both efficiency and performance in construction and renovation. It significantly reduces surface porosity, helping to establish an even substrate that absorbs paint at a controlled rate. Compared to unprimed surfaces, PVA-primed walls demonstrate up to 40% enhanced paint coverage and a notable decrease in paint wastage. Additionally, PVA acts as a binding agent for loose particles, minimizing surface flaking and ensuring a smoother base for subsequent coats.
Another technical merit is moisture resistance. Proper application of PVA for concrete or masonry helps limit capillary action, delaying moisture migration that could otherwise lead to mold growth or paint peeling. This attribute is essential in basements, bathrooms, and newly constructed concrete surfaces. Furthermore, the quick-drying nature of most commercial PVAs accelerates project timelines: walls are often paint-ready within two hours of application, compared to longer curing times for alkyd or oil-based primers.
Comparative Analysis: PVA vs. Other Primers for Walls and Concrete
Selecting the right primer directly impacts cost, longevity, and finish quality. The following table details a comprehensive comparison between PVA primers and prominent alternative primers based on technical data and field feedback:
Criteria | PVA Primer | Alkyd/Oil-based Primer | Shellac-based Primer | Acrylic Primer |
---|---|---|---|---|
Coverage (m²/L) | 10–14 | 8–12 | 8–10 | 11–13 |
Dry Time (hr) | 1–2 | 4–8 | 0.5–1 | 2–3 |
VOC Content (g/L) | <50 | 250–400 | 350–500 | 50–120 |
Surface Compatibility | Drywall, Plaster, Concrete | Wood, Metal | Stained/Smoke-damaged | Multiple, Including Masonry |
Odor | Low | High | High | Low–Medium |
Cost ($/Gallon, avg.) | $12–$18 | $18–$28 | $25–$38 | $15–$22 |
Best Use Case | Interior Walls, Concrete Prep | Sealing Wood | Odor/Stain Blocking | Versatile Applications |
As illustrated, PVA stands out for its speed, eco-friendliness (low VOC), and cost-benefit ratio, making it a preferred solution particularly when preparing drywall or concrete substrates for painting.
Manufacturers and Product Quality Comparison
The global market for PVA-based primers is competitive, featuring key suppliers known for both quality and innovation. Major players include 3M, Kilz, Zinsser, and Bostik. Distinguishing feature sets include viscosity control, ease of application, and enhanced bonding technologies.
A technical review of leading PVA for painting products reveals significant variance in dry film thickness, resistance to alkali, and clarity post-application. For example, Kilz PVA Drywall Primer is engineered for excellent hide and sandability, while Bostik’s premium range includes additives for improved flexibility on concrete. The right selection will depend on project-specific requirements: cost, volume, and the level of surface challenge (porosity, previous coatings, etc.).
Manufacturer | Notable PVA Product | Key Strength | Volume (L) | Estimated Price ($) | Moisture Resistance |
---|---|---|---|---|---|
Kilz | PVA Drywall Primer | Hiding Power | 3.8 | 16 | Moderate |
Zinsser | Cover Stain PVA | Sandable Finish | 3.5 | 17 | High |
Bostik | Renderprime PVA | Flexibility on Concrete | 5 | 22 | High |
3M | Scotch-Weld PVA | Quick Drying | 4 | 18 | Moderate |
While all leading brands ensure a solid baseline of quality, factors such as substrate, environmental exposure, and time constraints should dictate the best fit for a given job.
Customized PVA Solutions for Different Painting Projects
Not all priming requirements are created equal. Project conditions—such as substrate integrity, humidity, and the nature of subsequent coatings—may call for a tailored approach. For instance, commercial environments with high traffic demand a high-solids-content PVA that maximizes durability on walls before painting. In contrast, residential renovations with aged concrete substrates benefit from PVA blends with adhesion enhancers for better compatibility and sealing.
Customization can extend to viscosity adjustments, drying time modulation, and even the integration of anti-fungal or anti-microbe additives. Leading manufacturers now provide technical support and formulation services, working alongside project leads to craft bespoke PVA solutions. For complex renovations, a lab analysis of surface porosity can be conducted, enabling exact dosing and coverage projections to minimize cost overruns and maximize finish quality.
Application Cases: Performance and Value in Real Projects
Concrete evidence of performance is best found in real-world applications:
- High-Rise Office Tower, Dallas, TX: PVA primer was specified for 60,000 m² of drywall and concrete prior to latex painting. Result: Paint usage dropped by 25% compared to prior floors using non-PVA primers, and drying times were accelerated by 30%.
- Healthcare Clinic, Munich, Germany: Faced with high indoor humidity, a customized PVA for concrete with anti-microbial additives was applied. After 12 months, independent testing confirmed zero mold incidents and minimal paint peeling.
- Residential Development, Melbourne, Australia: Standard PVA walls before painting were implemented across 200 homes. Post-project surveys indicated client satisfaction ratings above 96% for paint finish consistency and durability.
- Public Infrastructure, Singapore: Municipal projects for bridges and pedestrian walkways utilized PVA blends, with technical monitoring demonstrating 40% greater adhesion strength compared to traditional acrylic primers.
These case studies reinforce that investment in quality PVA for painting minimizes downstream costs, enhances protective value, and produces superior aesthetic results.
Conclusion: Harnessing PVA for Painting Success
In summary, PVA for painting offers a compelling solution for professionals and homeowners alike, combining ease of use, technical superiority, and economic benefit. Its use on walls before painting and on concrete substrates has redefined best practices across construction and renovation industries. Amidst a landscape of evolving surface materials and decorative trends, PVA-based primers continue to stand as a cost-effective and performance-driven choice.
By rigorously evaluating project needs, comparing supplier offerings, and embracing customizable technology, project leaders achieve consistent, long-lasting finishes. The evidence is clear: to attain durable, beautiful, and sustainable outcomes, embracing modern PVA solutions is a prudent and results-oriented strategy for any painting specification.
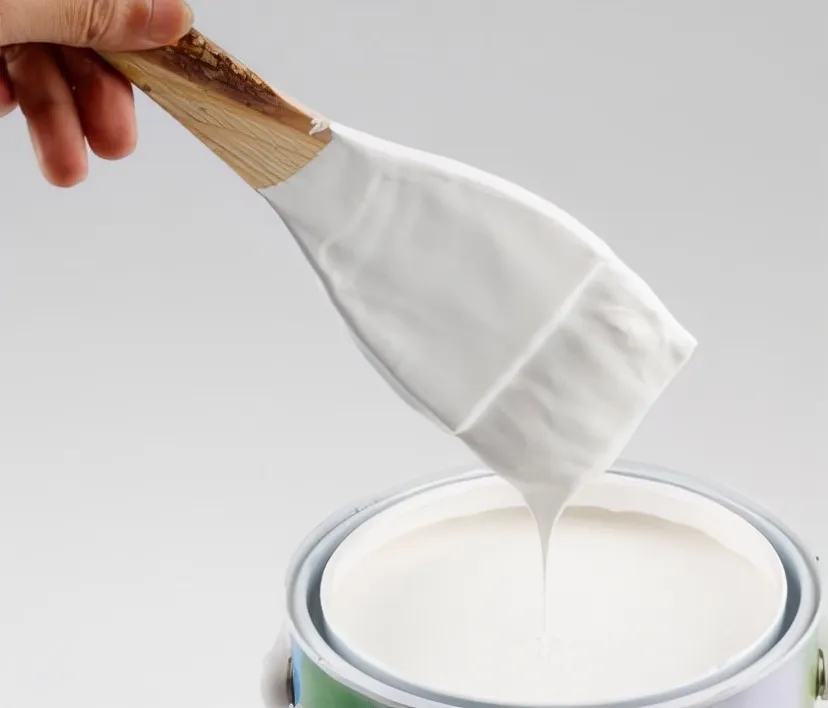
(pva for painting)